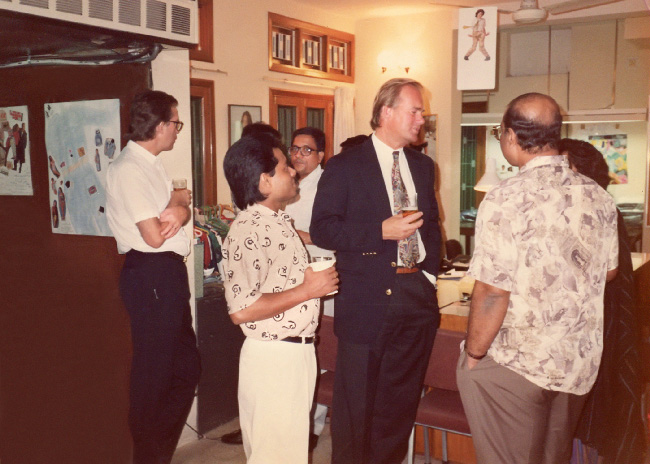
In conversation with Stefan Persson in the first Dhaka H&M office and Bjorn Palmqvist (left) who was the former Regional manager of Hong Kong when I was at H&M. My memory clearly states that he was saying to one of the leading manufacture (Right) that “Dhaka Liaison office is the Best Liaison office in H&M World” That made my chest wide and inspired to work harder motivation was running throughout my body. Stefan Persson is the current Chairman of H&M and this was his first visit to Bangladesh this office as well.
Mamun Kabir Bhuiyan
Managing Director & CEO
Technocraft World Corporation
Technocraft World wide Ltd
Dhaka , Bangladesh
Example of an World Class Lingerie Composite Factory
They were
setup as a fully vertical operation for the sole purpose of manufacturing high
quality brassiere. ALL specializes in brassieres using mostly in house fabrics,
narrow fabrics (elastics) etc. They produce a wide range of styles and designs
using a variety of fabrics, lace and accessories based on customer’s
requirement. The plant is fully equipped to produce high quality molded and
non-molded bra, with or without pad, with or without under-wire and bra with
traditional seams.
The total production capacity of the ALL for the different types of bra is 1.8 to 2.0 million pieces of bra per month. The production facility is sufficiently flexible to allow 15-20% additional capacity of any of the items.
Sports Bra
Pcs/month
|
Girls Bra
Pcs/month
|
Ladies Bra;
standard
Pcs/month
|
Ladies Bra;
fashion
Pcs/month
|
400,000- 450,000
|
500,000- 550,000
|
600,000- 650,000
|
300,000- 350,000
|
Facilities
within this Textile complex:
They textile
complex is the combination of these 3 vertical operations, from fabrics toGarment
factories along with Yarn Dyeing Mills. Most of the fabrics and other materials
for the garments are produced within the Textile complex. Items like lace,
under-wires, ring-slide and some special components are imported. Hangers, poly-bags,
printed individual boxes, woven labels etc. are locally available.
Each of the three garments factories; ASKML (knitwear),
ALL (Bra) & ATPML (underwear & knitwear) have separate and complete
set-ups for garment manufacturing, starting from design- sample-pattern to
garment finishing.
1.a. Sample, Pattern and design department:
The department in each of the garment manufacturing units
is equipped with CAD (Lectra and/or Garber) systems and between 60 to 80 sewing
machines to produce samples according to buyer’s specifications and /or own
designs. All samples are fitted on appropriate fitting-forms and on live models
before sending to the buyers. From digitized patterns, all production markers
are produced with optimum efficiency.
They mainly uses the
hook & eye tape making facility. This section is equipped with fully
computerized machinery to produce both hook tape and eye tapes of up to 4 rows.
The Hook & eye capacity is about 80,000 pieces/day.
Figure: Sections of sample, pattern
& design department
1.
b. Cutting department:
The cutting department for each of the sewing floors is equipped with fabric inspection, 8 to 12 cutting tables, straight knife, band knife and stripe fabric pilling or lace pilling setups. The capacities of each cutting departments are carefully matched with the respective sewing capacities, between 60,000 to 100,000 pieces each day. All cut pieces are checked and are prepared into bundles of 20 to 40 pieces. The bundle baskets are sent to the sewing section. Before cutting 100% of the fabrics are inspected and laid for sufficient time on cutting tables for relaxation.
The cutting department for each of the sewing floors is equipped with fabric inspection, 8 to 12 cutting tables, straight knife, band knife and stripe fabric pilling or lace pilling setups. The capacities of each cutting departments are carefully matched with the respective sewing capacities, between 60,000 to 100,000 pieces each day. All cut pieces are checked and are prepared into bundles of 20 to 40 pieces. The bundle baskets are sent to the sewing section. Before cutting 100% of the fabrics are inspected and laid for sufficient time on cutting tables for relaxation.
Figure:
Sections of the cutting floor
1.c. Sewing department:
All the sewing floors are equipped with modern apparel
machineries and attachments. The mechanical department is fully equipped with
specialized attachment making within facilities. The lines are laid out in a
manner to allow 100% inspection of the garments during production.
Figure:
Sewing Floor
1.d. Finishing department:
Completed garments in size lots are
cleaned of loose threads, dust etc. in vacuum suction device, as required.
Subsequently, the garments are transferred into an enclosed humidity controlled
(air conditioned) room, where, for the Bra and underwear, the garments are inspected
and for the knitwear’s, the garments are finished with steam iron on vacuum
tables. After putting all packaging accessories each piece is checked with
needle detector before packing for shipment. For all orders, internal AQL is
determined before buyer’s inspection.
Figure: Sections of the finishing floor
1. e. Molding &
Laminating:
They
mainly use the molding & laminating facility. This section is equipped with
foam molding, elastic fabric molding, rigid fabric molding, die-cutting (for
both foam & fabric) and fabric-fabric, foam-fabric, fiber fill-fabric
Laminating machinery. Foam molding Capacity: 52,000 pairs/day and fabric
molding capacity: 70,000 pairs/day.
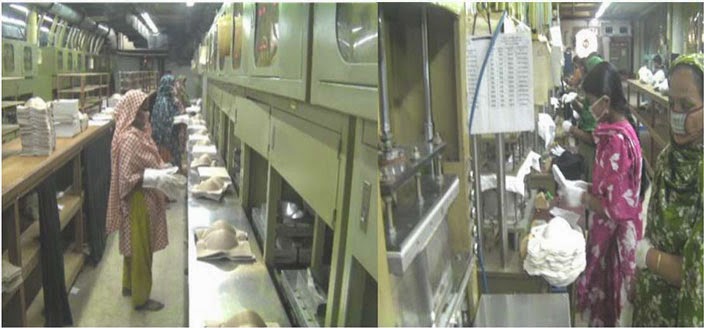
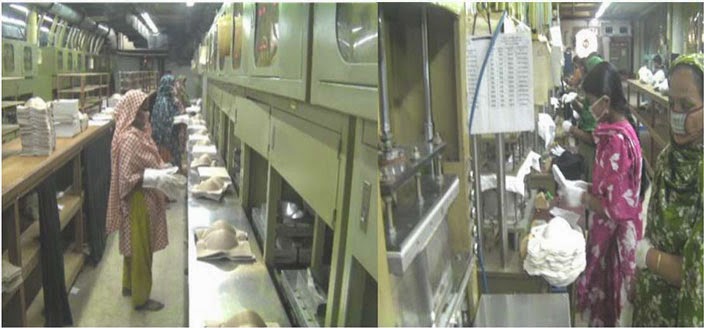
Figure: Foam & fabric molding
section
1.f. Hook & eye tape making:
A large
variety of wide fabrics (circular knit & warp knit), using a wide range of
fibers,100% cotton, polyester, nylon, various blends, micro-fibers with or
without spandex and yarn dyed or solid dyed fabrics are produced exclusively
for the garments units within the textile complex.
2.a. Wide Fabrics:
Circular knit fabrics:
There are a total of 145 circular knitting machines, most
of the machines are equipped with Spandex attachments and have extra-gauge
cylinders.
Circular knit fabrics can be solid
dyed or yarn dyed, with or without Spandex;
Total Capacity 3 5,000 Kg / day
·
Single
Jersey / Pique: Capacity/day:16,500 Kg
·
Interlock
/ drop needle: Capacity/day: 6,000 Kg
·
Rib
/ drop needle rib: Capacity/day: 6,000 Kg
·
Engineering
stripe (up to 6 colors): Capacity/ day: 1,500 Kg
·
3
thread fleece: Capacity/day: 5,000 Kg
Figure: Sections of circular knitting
department
Warp knit fabrics:
Solid dyed or yarn dyed, with or
without Spandex
v
Tricot:
Double tricot,
Charmeuse, mesh, honeycomb, velour, diamond tulle etc
(from rigid
to 30 % elastane); Capacity: 150,000 meters / month
v
Raschel:
powernet, satinette,
slee knit, one way stretch fabric etc
(from 5% to
35 % elastane); Capacity: 70,000 meters / month
v Simplex; Various types of Simplex fabrics (up
to 35% elastane)
Figure: Elastane warping, rigid yarn warping and
warp knitting sections
Flat knit fabrics:
Solid dyed or yarn dyed
v Collars / cuffs (SHIMA SEIKI); Capacity:
6,000 sets / day
v Fabrics for styling.
Figure
: Flat knitting section
2.b. Dyeing & finishing facilities for
wide fabrics:
v
Dyeing
machines are suitable for cotton, spandex cotton, polyamide, polyester,
viscose, and various blends; Capacity 55,000 Kg / day
v
14
sample dyeing machines which can produce 40 different sample fabrics in every
day.
v
This
department is equipped with both open width & tubular finishing machinery.
v
Fabric
finishing section is equipped with stenter / open-width dryer, tubular-dryer
Tumble dryer / open-width compactor / tubular compactor etc. suitable for
enzyme finish, silicone finish or any specialized finish (e.g., Teflon coating,
antimicrobial coating etc.); Capacity; 50,000 Kg / day.
v
In
addition to all the options for the chemical finishing, the department has
sued- / peach-finishing machines for mechanical finishes. Capacity: 5,000
Kg/day.
v
For
Fleece fabrics, the finishing section is equipped with raising machines,
brushing machine and searing machine. Capacity: 10,000 Kg/day.
Figure:
Sections of the dye-finishing
2.c. Printed Fabrics:
The printing section can produce about 50,000
meters/day of printed fabrics, with either reactive, disperse, acid or
pigment dyes.
The All Over Printing
(AOP) section is equipped with:
v
One
12 colors Rotary screen printing setup for knit fabrics with a capacity of
about 25,000 meters/day.
v
One
12 colors Flat-Bed printing setup for knit fabrics with a capacity of about
22,000 meters/day.
v
Loop
steamer / polymerizer / after print washing
v
Digital
engraving
v
Computerized
design preparation
v
Fully
equipped sample & strike off preparation
v
Color
kitchen
v
Screen
preparation, sample printing
Figure:
Screen preparation, sample printing and 12 color rotary screen printing
2.d. Narrow fabrics:
The narrow fabrics section is equipped with all the
necessary machinery to produce a wide range of elastic and non-elastic fabrics.
v
Rubber
covering (double covering): Capacity: 1200 Kg /day
v
Spandex
covering (single covering): Capacity: 540 Kg / day
v
Needle
looms (without jacquard): Capacity: 350,000 meters / day
v
Needle
looms (Jacquard): Capacity: 50,000 meters/day
v
Narrow
fabrics dyeing: Capacity: 350,000 meters / day
Figure: Yarn dyeing
section
Capacity 15,000 pieces/ day
v
Solid
Embroidery: 9 color machines
v
Embroidery
on print
v Sequence / cording /
boring
Figure: Embroidery section
5. Placement printing:
Capacity:
60,000 to 100,000 pieces / day in up to 6 colors
v Pigment / Discharge print
v Puff / Rubber print
v
Glitter
/ Flock print
v
Stone
attachment
v
Foil
printing / metallic shine
v
High
density printing
v
Photo
print
Figure: Placement printing.
6. Pad printing & label printing:
In keeping with the need of the market, they has setup
the facilities to print labels on
label tapes as well as printing labels (particularly care
labels on bra and underwear)
on the body of the garments, using both pad printing
machines or using transfer print
labels.
7. Washing plant:
Capacity 25,000 pcs garment / day
The washing plant is equipped to wash knit garments with
various additives enzymes during wash and also during the drying cycle.
Figure: Section of the garment washing
plant
8. Packaging & Store:
All garments are fully inspected & packaged before
inspection by buyer or buyer’s agent.
A large area is allocated for the proper storage of the boxes before shipment.
Figure: Packaging & Store
9. Quality control & Textile
testing
In addition to the modern machinery & equipment’s, they
have constantly worked with a wide range of technical experts from Japan,
Philippines, Hong Kong and Sri Lanka to improve the working and quality control
procedure. Sewing technicians work constantly with the operators and supervisor
to upgrade the quality standards and optimize efficiency.
v
QA
department personnel conducts inspection of fabric, cutting, molding, bundle
preparation and 100% garment quality inspection and recording at all stages of
production as per requirements by the buyer.
v
Fabric
weight (density), yarn count & composition
v
Spectral
color matching
v
Color
Fastness to wash, Rub, light etc.
v
Shrinkage
and other dimensional stability
v
Extension
and Modulus etc.
Figure: Section of laboratory,
Spectral equipment and OEKO-TEX certificate.
In addition, regular
testing of yarn, fabrics etc. are conducted at our well-equipped lab, Accredited
by World class Buyer.
10. Product Development and Fashion Design
Department:
For the last several years, they product development team
has been working with various buyers to develop new fabrics, prints, narrow
fabrics, embellishments’ etc. to create new fashion garments for the export
market. Based on this experience, in 2010 they setup a new independent department
for this purpose, staffed by Textile engineers, fashion designers and a
complete sample sewing section. The textile engineers in conjunction with the
R&D and fabrics departments develop new fabrics, elastics, prints and other
embellishments. Fashion designers use these to develop fashion products for the
various export market. This has proven to be very useful to the buyers from USA
and Europe and many of them are routinely using this facility.
11. Conformity with International Labour
& Environmental Standards:
Their operations are conducted with awareness for
environmental safeguard and we deem it as their obligation to prevent pollution
by complying with relevant environmental legislations. They are one of the
country’s very first textiles knit composite industries to have its own
Effluent Treatment Plant (ETP) with a daily capacity of 8 million liters/day. They
fully treats all factory effluent before releasing into the environment. All
the factories within the complex are fully compliant with and or certified by;
v
WRAP
certified
v
OEKO-TEX
Standard 100
v
OE
(Organic Exchange Certificate)
v
GSV
/ CTPAT approved
v
Fare
Trade
v
ISO
9000 2001
v
SEDEX
v
Code
of Conduct required by major retail stores of the world.
They
follow ethical employment practices and adhere to applicable state, National
and International laws on labor employment. They provide a clean, safe and
healthy environment, adopt fair labor practices, reward them with wages without
any discrimination and they do not interfere in their freedom of association
and personal freedom. In addition, they have the Child care center accommodate
with 90 children providing food, nursing etc.
12.
Delivery time and other Commercial issues
Typically an order can be made ready for shipment in
30-90 days depending on approvals of the buyer. Prior to the confirmation of an
order, order details and buyer’s desired delivery dates are sent to the PPIC
(Production Planning and Inventory Control) department. Upon receiving the export
Letter of Credit or Contract, There merchandizing and commercial department
issues purchase orders for the required raw materials. After supplier
confirmation of shipment date(s), PPIC department confirms production plans.
The production management team, PPIC department, and QAD coordinate the
production and the commercial department oversees the export and documentation.